表面粗さ
日頃より本コンテンツをご利用いただきありがとうございます。
今後、下記サーバに移行していきます。お手数ですがブックマークの変更をお願いいたします。https://kousyou.synology.me
表面粗さについて
表面粗さとは部品を加工したときの加工面の表面の 状態を示すものです。 同じ機械で加工しても、荒取り(一度に深く加工をする 、送り速度が速い加工)、 仕上げ加工で 面の状態は 違ってきます。 しかし ある機械ではどうしても超えられない精度が あります。たとえば 旋盤では、研磨盤のような研磨 した面は加工できません。 従い この表面粗さ指示により 加工者はどのような 段取りで加工するかを決定する重要な指示になります。
種類 | 記号 | 求め方 | 説明図> |
中心線平均粗さ(特別に指示が無ければ通常この 方法で示されます。 | Ra | 粗さ曲線を中心線から折り返し、その粗さ曲線と中心線によって得られた面積を長さLで割った値をマイクロメートル(μm)で表わす。 | ![]() |
最大高さ | Rma | 断面曲線を基準長さLを抜き取った部分の最大高さを求めてマイクロメートル(μm)で表わす。傷とみなされるような並はずれて高い山や深い谷のない部分から、基準長さだけを抜き取る。 | ![]() |
十点平均高さ | Rz | 断面曲線から基準長さだけを抜き取った部分において、最高から5番目までの山頂の標高の平均値と、最深から5番目までの谷底の標高の平均値との差の値をマイクロメートル(μm)で表わす。 | ![]() |
表面粗さの種類と区分値および三角記号の区分
中心線の平均粗さ | 十点平均高さ | 最大高さ | 三角記号 | Ra記号 | 適用 | 加工法 | ||||||||||
Ra | Rz | Rmax | ||||||||||||||
基準長さ(ミリ) | カットオフ値(ミリ) | 標準数列 | 標準数列 | 基準長さ(ミリ) | 基準長さ(ミリ) | 標準数列 | 仕上げ記号 | 仕上げ記号 | ||||||||
カットオフ値の3倍以上 | 0.8 | 0.13a | 0.05z | 0.25 | 0.25 | 0.05s | ▽▽▽▽ |
|
鏡面、びっちりした摺動面 | 研磨研削 |
||||||
0.025a | 0.1z | 0.1s | ||||||||||||||
0.05a | 0.2z | 0.2s | ||||||||||||||
0.1a | 0.8z | 0.8s | ||||||||||||||
0.2a | 0.8z | 0.8 | 0.8 | 0.8s | ▽▽▽ |
|
信頼性を必要とする摺動面など | 研削 | ||||||||
0.4a | 1.6z | 1.6s | ||||||||||||||
0.8a | 3.2z | 3.2s |
|
ハメアイ、接触面、ベアリングケース | 切削 | |||||||||||
1.6a | 6.3z | 6.3s | ||||||||||||||
3.2a | 12.5z | 2.5 | 2.5 | 12.5s | ▽▽ |
|
接触面 | 切削 | ||||||||
6.3a | 25z | 25s | ||||||||||||||
12.5a | 50z | 8 | 8 | 50s | ▽ |
|
一度削った表面 | 切削 | ||||||||
2.5 | 25a | 100z | 100s | |||||||||||||
50a | 200z | 25 | 25 | 200s | ― |
|
素材面 | |||||||||
100a | 400z | 400s |
表面粗さ指示の考え方
上の定義の解説では、非常に難しくよくわからないと言うのが、と言うか、ここまで厳密に加工(測定、管理)されているのかといえば、していないのが現実でしょう。
するとすれば大量生産する部品で特に その機械の中心的役割を担う重要部品のはずです。
設計の立場から言えばこの面は、こんな機械でこの程度まで仕上げてくださいね。と言うことで、加工する側もこの記号の場合は、こんな機械が必要だな~と理解するものです。
ほとんどの場合 切削までで、要件はみたしますが、面と面が強くこすれる場合、摺動面、圧入などは研磨しておかないと面そのものが毛羽立つ感じで剥離が起こります。 その場合は研磨まで行います。
これも公差と同じで前例に倣うと言うことが一番 確実になります。 今でも 多くの図面が三角記号を使用しています。(私が関わっている業界が特別かもしれませんが)
JISではもう20年以上前からRa記号を推奨していますがなかなか 切り替わって行かないのが実状です。
ここからも 多くの人が 数値ではなく一つ山は荒取り、二つ山は 切削の仕上げ 三山は切削の仕上げもしくは研磨と言う感覚で理解していることがわかります。
ちなみに 研磨する場合は 三角記号の上に G を追記します。 説明: このようにです。
Ra記号の基本形状は以下の意味を表し そこへ粗さ範囲の数値を付加して表す。
左のような加工せずに面粗さ数値のある指示はあまり 見た記憶はありません。 通常は右にある加工ありで数値ありでしょうね。
Ra以外の指示は左のようにどの測定方法か解るように記号を付加します。
面粗さ数値以外にも左に示すような指示も付加される場合があります。
部品図面枠内には。必ず左のような面加工指示が必要です。
カッコ内は、この図中のどこかにこの面指示記号があることを示しています。
指示のない面についてはすべてカッコ外の指示に従うということになります。
カッコの中が空欄でカッコ外に加工ありとなるものもあります。
表面粗さを10μm Rmaxとか1μm Raなどと数値で表示するためには、専用の表面粗さ測定機を必要とします。 そこで加工中の簡易的な測定のた めに図28に示す比較用標準粗さ試験片が用いられます。
これは、フライス盤用です。
これは旋盤用です。
爪の先で試験片と工作物を交互にひっかき 工作物と良く似た感触を受ける試験片の粗さが、 おおよその表面粗さを表します。
右は各、加工方法において表面粗さと相対コストとの関係を 示したものです。
たとえば, 表面粗さとして10μmより大 きい値が許されるときは切削加工が適当であり、また1μm 前後の仕上げ面が要求さ れる場合は研削加工が経済的であり、さらに0.1μmにするためには、ラップ仕上げが経済的です。
加工方法による面粗さの範囲を下記に示します。
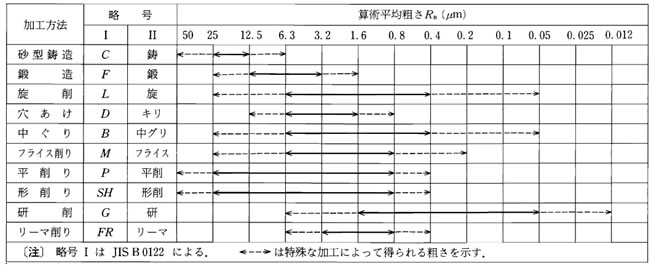
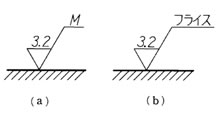
研磨と研削は、ほぼ同意語ですが、私の認識では、研磨は研削を含むもので、特に研削というと砥石を使用した加工のこと、研磨とはラップ仕上げのように繊維系の研磨剤で仕上げるものです。
多くの場合面粗さが細かくなるほど精密度が増し、加工時間も多くかかります。 従いコスト面からそれほど精度を必要としない箇所は必要最低限の面粗さで加工は完結します。
しかし中には、特別に粗い面が必要なケースもあります。 紙送りなどの摩擦抵抗を大きくしたい場合などです。 そのようなケースで粗さを指定されると加工が難しくなります。
なぜかと言えば 通常の機械加工ではRa5.0と指定された製品をRa1.0の製品を納入してもクレームはつきません。
不精密でよい製品に精密製品を代替えで納品しても問題にはならないことが多いからです。
粗い加工をある範囲内に入れることは精密面を加工するよりも難しいのです。
これは、放電加工機で電流値等を条件を試行錯誤して作成した粗さサンプルです。
粗さサンプル写真 これはフライス&研削盤で加工した試験片です。
フライスで粗さ精度(決められた範囲)を確保するためには下の例のような1枚刃で加工します。
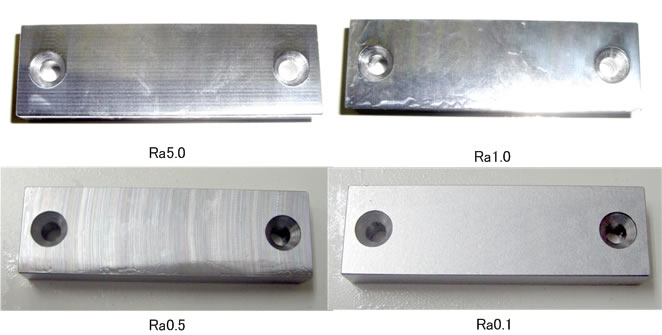
専用刃物でRa5.0を加工します。 Ra1.0以降は研削加工をします。
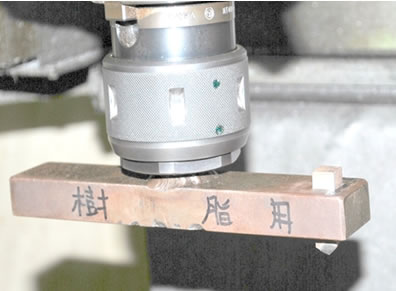
面粗さ測定装置で測定したデーターサンプルです。 粗さ測定データーサンプル
表面うねり
表面粗さより大きい間隔で繰り返される起伏を表面うねりと言います。
表面うねりは表面粗さを指定するだけでは、満足できない高精度の仕上げ面を要求する場合に必要です。
うねり曲線は表面粗さ曲線を除去して求めらられます。
(a) 断面曲線 測定断面曲線にカットオフ値λ s の低域フィルタを適用し て得られる曲線
(b)粗さ曲線 カットオフ値λ c の高域フィルタによって、断面曲線から 長波長成分を遮断して得た輪郭曲線
(c)うねり曲線 断面曲線にカットオフ値λ f 及びλ c の輪郭曲線フィルタ を順次かけることによって得られる輪郭曲線。λ f 輪郭曲 線フィルタによって長波長成分を遮断し、λ c 輪郭曲線 フィルタによって短波長成分を遮断
カットオフ値
断面曲線からフィルターを通して波長を取り除くことを「カットオフ」といい、粗さ成分と、うねり成分を区別する分岐点の波長を「カットオフ値」といいます。
“うねり”成分を除くために使用されます。 表面粗さの大きさにより使用されるカットオフ値を定めています。